What is a Plate Heat Exchanger
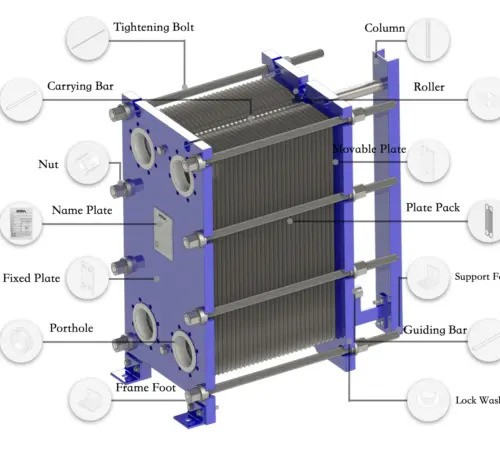
Put simply, a plate heat exchanger (PHE) is a highly efficient device that consists of multiple heat transfer plates held in place by a fixed and a loose pressure plate. The gasket arrangement on each heat transfer plate provides two separate channel systems that enable the primary and secondary media to flow in a counter-current manner without mixing. This feature, coupled with the corrugated plates that create turbulence in the fluids, results in an effective heat transfer coefficient.
The plate heat exchanger (PHE) design consists of multiple heat transfer plates, secured by a stationary and a movable pressure plate, forming a comprehensive assembly. Each heat transfer plate features a gasket system, which provides two independent channel networks. The gasket arrangement allows for through-flow in single channels, facilitating counter-current flow of primary and secondary media while preventing their mixing due to the gasket design.
The turbulence caused by corrugated plates as fluids course through the assembly increases the effective heat transfer coefficient, enabling efficient thermal exchange. HFM has an extensive range of plate heat exchangers designed for various industries and applications, catering to heating, cooling, heat recovery, condensation, and evaporation.
How Does a Plate Heat Exchanger Work
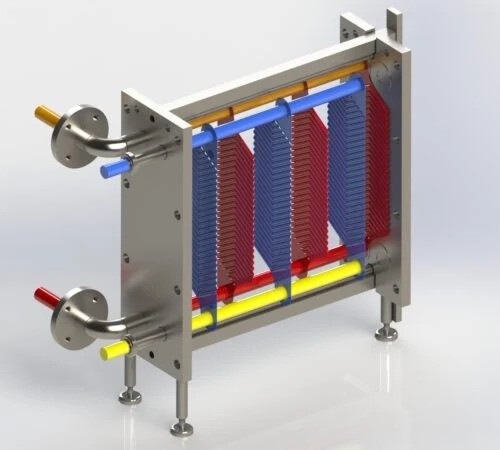
Gasketed Plate Heat Exchangers (GPHEs) are designed to optimize heat transfer between two fluids or gases. The corrugated plates within the Gasketed Plate Heat Exchanger allow for efficient heat transfer from one medium to the other.
The plates used in Gasketed Plate Heat Exchanger are equipped with elastomeric gaskets that seal the channels and direct the mediums into alternating channels. The plate pack is placed between a frame plate and a pressure plate and compressed using bolts between the plates. An upper carrying bar supports the channel and pressure plate, which are then fixed in position by a lower guiding bar on the support column. This design facilitates easy cleaning and modification by adding or removing plates.
4 Main Types of Plate Heat Exchanger:
When it comes to plate heat exchangers, there are four primary types optimized for efficient heat transfer across various industrial applications. These versatile devices play a crucial role in optimizing heating and cooling processes
- Gasketed Plate Heat Exchangers:
- Brazed Plate Heat Exchangers:
- Welded Plate Heat Exchangers:
- Semi-Welded Plate Heat Exchangers:
Gasketed plate heat exchangers, known for their reliable sealing, are designed to facilitate effective heat exchange. They employ high-quality gaskets to ensure a secure seal, preventing any potential heat loss or leakage. The flexibility of these exchangers makes them ideal for applications requiring precise temperature control and efficient heat transfer.
In demanding industrial environments, brazed plate heat exchangers excel in delivering high heat transfer rates. Their compact design and efficient heat exchange capabilities make them a cost-effective solution for heating and cooling processes. When constructed with stainless steel plates and copper brazing, these exchangers exhibit exceptional resistance to corrosion, ensuring longevity and reliability.
Designed for heavy-duty applications involving high temperatures and corrosive substances, welded plate heat exchangers provide robust and durable heat exchange solutions. The welding of plates creates a secure and leak-proof configuration, making them suitable for critical processes that demand reliable and efficient heat transfer.
Combining the advantages of both welded and gasketed plates, semi-welded plate heat exchangers are engineered to balance efficiency and serviceability. These exchangers feature pairs of plates that are both welded and gasketed, offering an optimal solution for applications requiring precise control over heat transfer and temperature regulation.